在化工和农业制造行业,选择合适的传统维护方法与技术驱动的可靠性解决方案相结合,对于提升绩效和增加经营利润率至关重要。
原文:Tech-enabled asset productivity in chemicals and agriculture | McKinsey
在这些行业中,卓越的维护和可靠性管理能够创造巨大的价值。例如,在典型的化工厂中,固定成本中有大约50%与维护相关,而计划外的停机往往是导致生产损失的主要原因。
那些在维护和可靠性管理方面做得好的化工企业,不仅能提高盈利能力(增加4%到10%),还能提高资产负债表的效率,减少冗余和计划外的停工(设备综合效率OEE提高7%到13%)。此外,可靠性高的工厂通常还拥有更高的经营利润率和更佳的安全记录:非计划维护事件减少7%到16%,安全绩效提高20%到30%,成本降低20%到30%。
然而,成功实施维护和可靠性转型并非易事,尤其在当前形势下更显困难。普通工厂常常因计划外的维护而负担重重,其成本是计划维护的三到五倍。在过去30年中,资产的平均寿命翻倍,这直接导致了维护成本的上升。同时,庞大的维护团队不仅要处理复杂的工作流程,还要使用过时的系统,他们大量时间花在价值较低的活动上(化工和农业领域的典型工作人员实际操作时间不到30%)。此外,随着许多熟练工人的退休(未来三到五年内将有27%的劳动力退休),将面临知识流失和生产力下降的风险。最后,许多目前实施的数字化解决方案,虽然最初被宣传为能够迅速提升生产力,但由于系统间不兼容、用户界面不友好以及糟糕的计划和集成执行,最终效果往往令人失望。
总之,为了实现更高级别的维护和可靠性绩效,选择正确的资产生产力方法是至关重要的,这需要结合经典的精益思维和适当的数字化工具(如下图)。
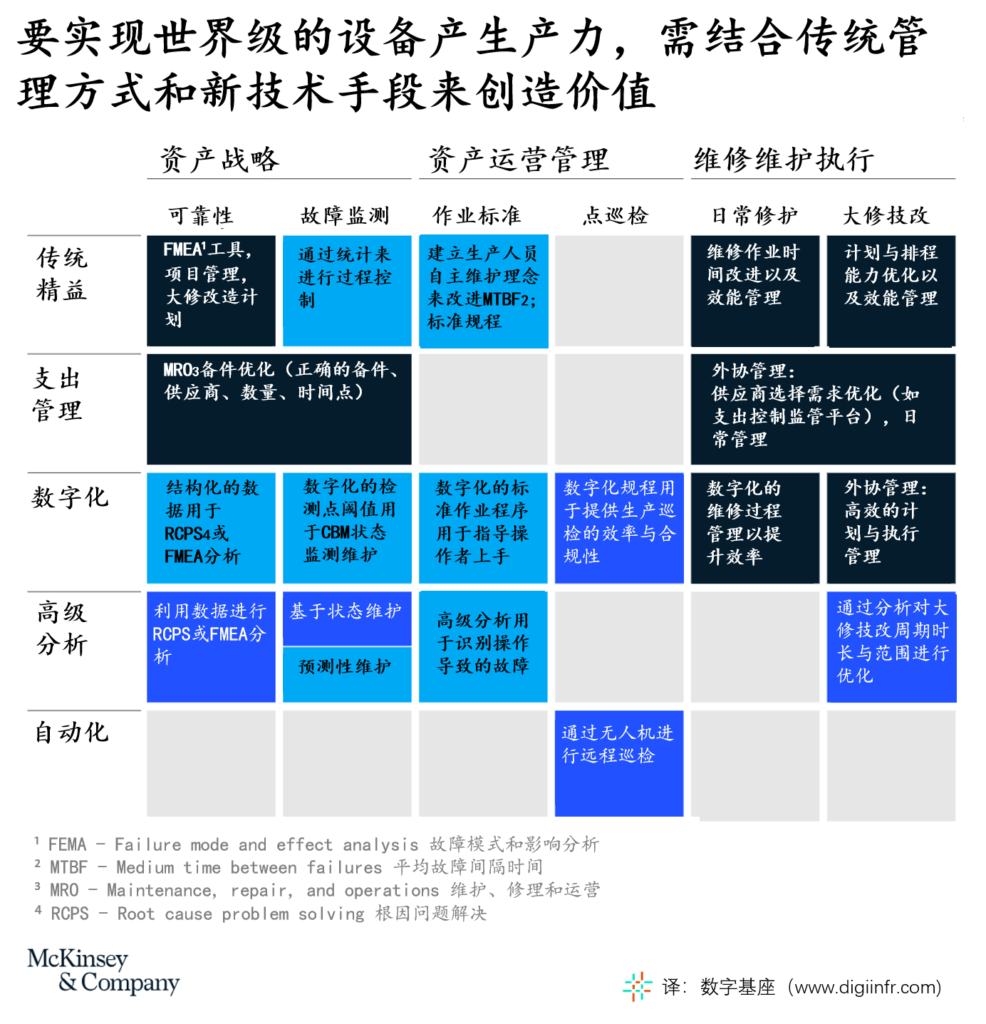
在提高传统精益基础和支出管理方面,潜在的影响极大,因此这些领域应成为改进的首要目标。其他重要领域包括为可靠性分析配备合适的人才,以及在工作执行计划和调度上进行额外的投资。基于坚实的精益基础,数字化和分析工具能够帮助实现并持续提升精益生产力,而基于状态的维护则有助于预防故障。此外,如果有足够的数据支持高级分析算法的开发,并且故障成本足以证明投入的必要性,通过机器学习进行故障预测也可能为某些资产创造价值。
选择正确的改进方法需要全面了解面临的问题。寻求改善维护和生产力的公司通常面临以下三种情况之一,每种情况都需要特定的策略:
- 快速成本降低:这种情况通常发生在迫切需要降低成本以提高竞争力的情况下。它涉及到消除低价值任务,提高执行效率,以及更好地选择和管理承包商和备件。
- 增加产品销售:如果有机会销售更多产品,公司可以专注于最大化关键资产的可靠性,尽量减少计划外和计划内事件的发生,并提停机检修计划和执行的整体效益。
- 数字化卓越:适用于已经掌握了传统精益基础并希望借助数字化和分析实现更高水平生产力的公司。成功需要识别和部署正确的数字化工具,同时避免试点得不到推广或是冗长的实施时间表。
例如,一家大型全球化工生产企业之前过分关注短期成本削减,导致了被动式维护文化。这种做法结果导致可靠性不足,错过生产期限和未能满足客户承诺。频繁的机械故障使计划工作几乎不可能执行,调度方法平庸导致执行效率低下,有效维修作业时间仅为15%到20%。由于预防性维护没有按时进行,导致了超过30周的工作积压,难以管理,设备的可预测性差,频繁故障限制了生产能力。
该制造商采取了两步解决方案来大幅提高效率和有效性。首先,它重新设计了管理流程(优先级排序、控制和计划),并明确定义了维护和可靠性相关负责人。其次,采用了数字化工具来改善工作调度、跨职能协调和任务速度。
这种传统与数字化手段的结合带来了快速的改善效果。计划和调度生产力提高了30%,有效维修时间提高了2.5倍。工作积压减少到不到两周,预防性维护合规性大幅提高,非计划停机时间减少了近10%。随着设备可靠性的提高,客户满意度也随之提升。因此,工厂重新获得了销售团队对其满足需求和承担更多产能的信心。