新技术正在深刻改变售后服务行业,不仅让客户获益,也为服务提供商创造了新的机遇。
原文:The coming evolution of field operations | McKinsey 译:数字基座#无边界技术
想象这样一个场景:周四下午,您接到一条基于设备传感器的警报,提示客户工厂的一台关键设备即将停机。如果不及时处理,客户可能会遭受数百万元的损失。在短短几分钟内,您从市场上找到了合格的设备专家,并迅速安排他们前往现场。客户可以通过手机应用实时查看技术人员的位置。
技术人员在赶往现场的途中,就能通过传感器进行远程诊断,无需等到现场才能确定问题。他们已经明确了具体故障、修复方法以及所需的零件和工具。到达现场后,技术人员使用增强现实工具,并在总部专家的远程指导下,一步步完成维修工作。更值得一提的是,团队还发现了设备的另外两个潜在问题,并主动进行了修复。从收到警报到解决问题,整个过程不到四小时,客户对此非常满意。
这就是未来现场运营服务的样貌。面对新技术和先进分析方法带来的变革,那些拥有售后服务的优秀工业制造商并不是抵制这些趋势,而是积极利用它们。这些公司正在改革他们的现场运营,以显著提升服务水平和客户体验,提高效率和生产力,并为客户和自身(作为设备原厂商,OEM)创造新的价值。
根据我们的经验,利用新技术改革现场团队的企业,在劳动成本、生产力和其他绩效指标方面都能取得显著成效。(图1)
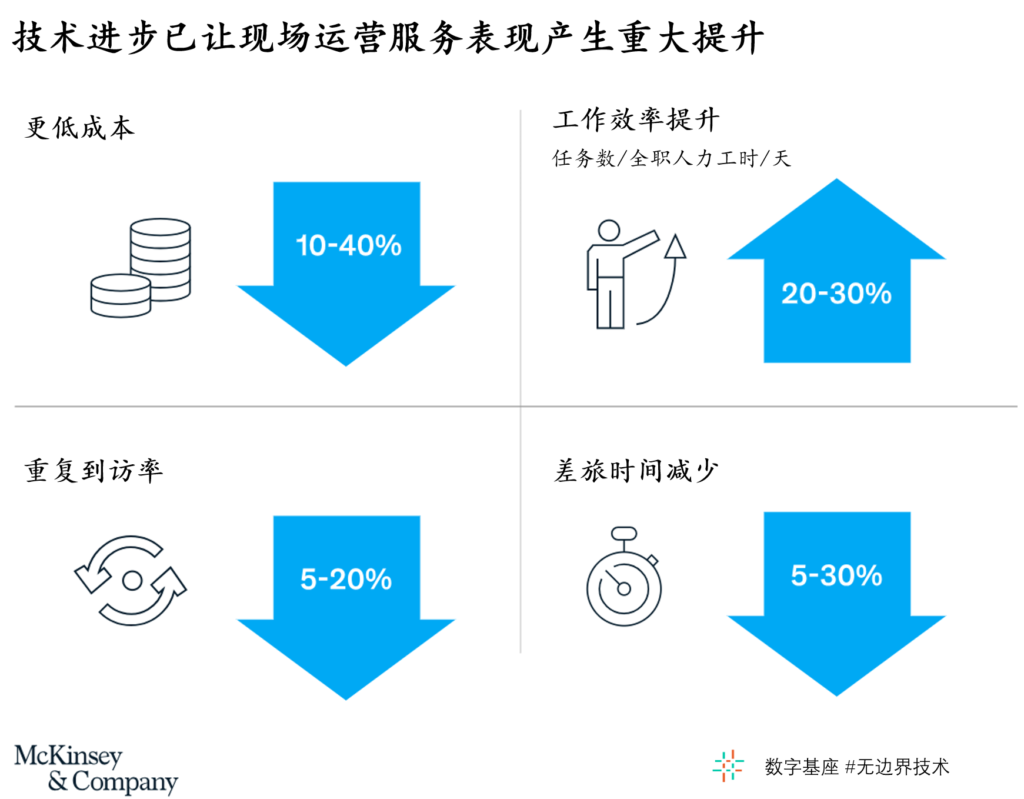
四个基于技术的重要趋势
近几十年来,现场运营职能一直随着技术的发展而不断演进。然而,新兴技术的出现意味着现场服务将在效率、效能、生产力和客户体验等方面实现质的飞跃(图2)。
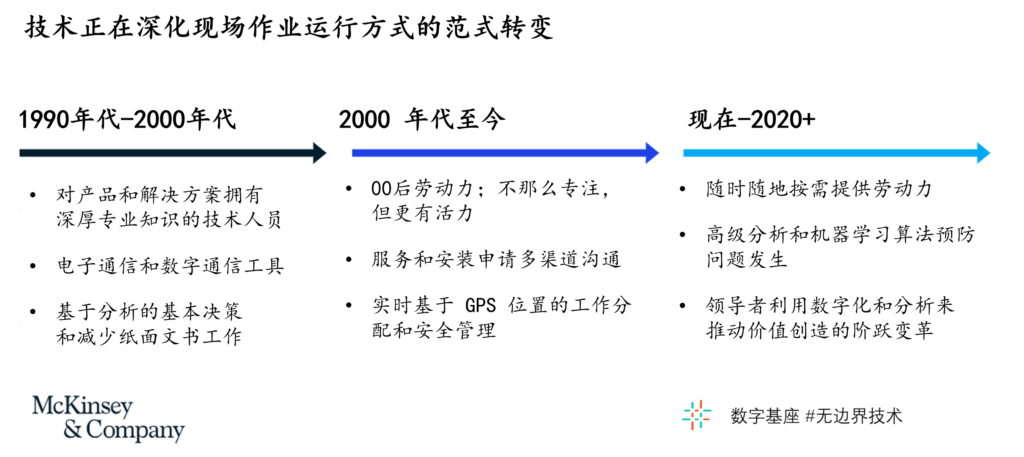
更智能、更集成的工作流程工具
过去,公司致力于将信息汇总到仪表板中。虽然这是一个良好的开端,但仪表板存在诸多缺点:数据过多却缺乏洞察,难以有效管理,且报告周期通常较慢,一般为每周或每月。
相比之下,先进的分析技术允许公司根据跟踪的信息生成具体的行动步骤。这些步骤通过智能行动板呈现,提供非常具体的指导,甚至可以细化到个别员工的辅导、跟进特定客户以解决低满意度问题,或访问设施以处理服务水平协议的失误。这种方法的优势在于,它省去了在仪表板上手动分析数据并据此决策的步骤。相反,行动看板为经理提供了明确的行动路线,通过标准化的措施确保所有经理都能一致有效地行动。更重要的是,这种方法允许公司实时响应指标。
人工智能和机器学习
人工智能和机器学习使预测性维护变得更加高效。嵌入式传感器和其他工具使制造商能够实时跟踪所有实物资产,所有警报都可以在一个屏幕上一目了然。详细视图提供了机器性能的关键指标,使制造商能够立即创建服务工单并提供可能的解决方案。
当设备发生故障时,人工智能和机器学习可以帮助技师缩短诊断时间。例如,更智能的物联网应用可以为技术人员提供单屏集中视图,显示所有必要的服务要求和特定任务的详细信息,以及易于访问的知识文档,以快速处理服务申请。技术人员还可以获得按需支持,并与远程经验丰富的技师并行工作,后者可以指导他们完成复杂的维修过程。一家全球装备设备企业采用这种方法,为全球约25,000名现场技术人员提供支持,整个组织的维护成本降低了15%。
增强现实(AR)
最简单的AR形式是技术服务人员手中的平板电脑。设想一位技师在现场需要修理电路板,但不知道如何操作。传统做法是查阅手册并开始排查故障——这可能会浪费时间,或者让调度员派另一位更专业的技术人员前来,导致持续停机和不良客户体验。
而使用AR功能的平板电脑、眼镜或其他工具,技术服务人员可以获取有关故障设备的更多信息。例如,使用耳机的可以不占双手,同时处理维保任务。越来越多的先进AR工具正在问世,它们可以让工人将平板电脑对准机器并下载内部示意图,使服务技师在拆开设备之前就能看到内部的预期样子。AR的一个常见应用是允许技术服务人员从总部的远程专家那里寻求帮助,后者可以通过AR增强视图中的可视步骤指导现场技师。这种方法能加快问题解决速度,提高客户体验。从半导体和高科技到石油和天然气以及重型设备,各个行业的公司都在为其现场技术服务人员采用AR应用。
按需劳动力
技术正在改变现场组织的劳动力配置方式。公司不再需要维持一整套全职员工队伍,而是可以使用按需人员配置来降低劳动力管理的复杂性。这种”滴滴式”的人才模式让技术工人(如认证技师、程序员、电工和其他专家)可以通过按需市场提供服务。对于原始设备制造商(OEM)来说,这种方法可以优化劳动成本,特别是在非核心任务。公司还可以简化支持功能,同时提高服务水平并扩大服务覆盖范围。
将技术工具付诸实践
企业需要综合运用各种工具和方法。以下是一些现实世界中的应用案例:
- 匹配需求:许多装备制造商难以准确预测需求。通过使用机器学习等先进分析工具,他们可以整合多个数据来源(包括内部和外部数据),为每个本地市场构建准确的需求预测。此外,他们可以通过按需劳动力资源设置合适的内部员工水平,灵活调整人员配置。同时,他们还可以设置动态调度系统,快速派遣现场技术人员到工作现场,并能实时响应变化。总体效果:劳动成本降低5-20%。
- 提高效率:通过自动化和数字化流程,装备制造商可以更高效地运营现场操作。例如,将手动流程和纸质文档数字化,用智能设备替代传统剪贴板。他们还可以使用高级分析来梳理工作报告并识别最佳实践,然后在整个组织中推广这些标准化实践。同时,确定关键绩效指标并创建行动导向的仪表板,以更好地管理绩效。总体效果:生产力提高10-30%。
- 改善客户体验:装备制造商可以利用新技术改善客户体验。例如,应用分析技术识别整个客户旅程中最重要的满意度驱动因素,从而消除痛点并优化服务。他们还可以利用分析提高服务到销售的转化率。总体效果:销售额增加5-15%,客户满意度提高20-40%。
以一家电信公司为例,该公司在运营现场服务时成本高昂。更糟糕的是,在技术人员利用率和按时完成客户预约等关键绩效指标上,落后于竞争对手。问题的根源在于不同部门(销售、预测、调度和现场操作)各自为政,只专注于自身工作而忽视了真正的客户服务目标。为解决这一问题,公司建立了一个协调机制,使所有部门能够近乎实时地协作。这使得组织在劳动力调度上更加灵活,确保每个人都对绩效负责,关注最终客户,并持续改进现场操作。最终结果是,组织提高了现场技术人员的生产力10%,按时完成预约的比例提高了5%。
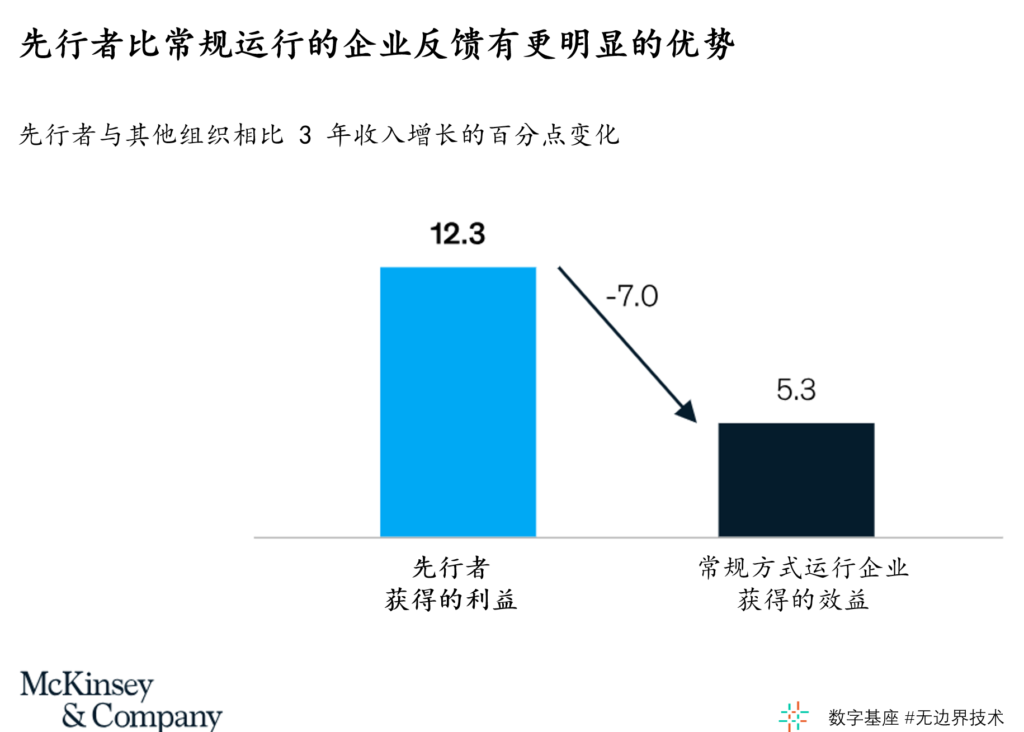
管理的四个优先事项
为充分利用新技术,装备制造企业的领导团队应重点关注以下四个方面:
- 提升数字和分析能力:许多企业在这方面还有欠缺。装备制造商需要有计划地提升这些能力,可以通过为现有员工提供培训和发展计划,或者有针对性地招聘新人才来实现。
- 加强与解决方案提供商合作:装备制造商应主动与开发新工具的供应商合作。这不仅有助于了解行业未来发展趋势,而且由于解决方案提供商往往缺乏特定行业的实践经验,他们也会欢迎终端用户的意见和专业知识。
- 更新员工思维模式:装备制造商应营造持续改进的文化氛围,可以通过建立奖励和激励机制,鼓励技术人员和一线员工分享改进建议并分享由此带来的收益。
- 重构组织架构:许多装备制造商的组织结构是为传统运营模式设计的。数字化和先进分析技术能显著改变工作流程——优化某些流程,甚至完全取代其他流程。企业需要调整组织结构,以充分发挥这些技术的潜在优势。
实例分析:
一家全球装备制造商在设备维护请求的周转时间上遇到了困难。公司发现问题的根源在于诊断过程耗时过长,以及派遣到现场的技术人员往往缺乏解决实际问题所需的技能或零件。事实上,该公司已在部分设备中嵌入了可捕获性能数据的传感器,但这些信息被发送到一个无人问津的数据库中。为改善这一状况,公司组建了一个分析团队,负责开发机器学习算法,以识别关键设备最常见的故障及其主要原因。利用传感器数据,该团队开发的算法能以75%的准确率预测设备故障的前三大原因,显著提高了一次修复率。
结语
如今,设备可以远程报告其状态并提供修复建议。数字化和高级分析技术已在实际应用中证明了其有效性,前瞻性企业已开始使用这些技术。这为公司提供了提升性能、降低成本和增加客户满意度的明确途径。唯一的不确定性在于管理团队是否有远见开始利用这些工具,还是将未来的机遇拱手让给竞争对手。