前言
在现代工业生产中,设备是创造价值的核心。如何确保设备“安、稳、长、满、优”地运行,是所有企业追求的目标。从“坏了再修”的事后维修,到“定期大修”的计划维修,再到今天我们广泛应用的“点-检定修制”,设备维修理念经历了一系列深刻的变革。点检定修制不仅是一种维修方法,更是一套科学、系统的设备管理哲学。本文将深入探讨其起源、在中国的发展历程、应用误区,并展望其在智能化时代的新篇章。
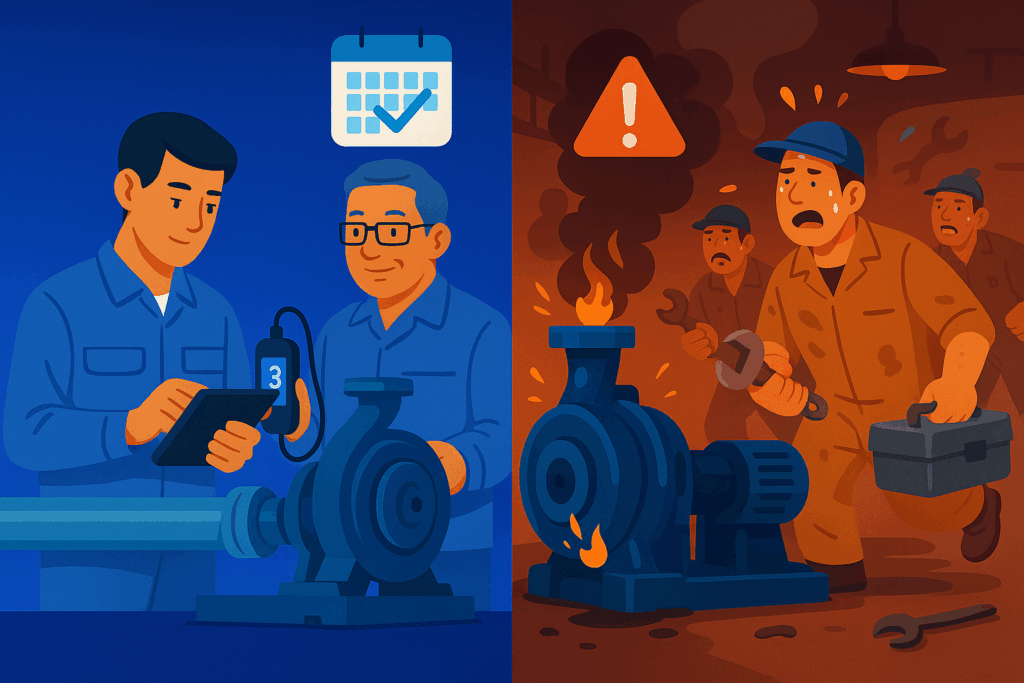
1. 什么是点检定修?—— 现代设备管理的基石
点检定修制是一套以“点检”为基础,以“定修”为手段的设备维护管理体系。其核心思想是:通过对设备的状态监测(点检),准确掌握其劣化程度,并依据数据分析,科学地制定维修计划,在恰当的时机进行预定性的修复或更换(定修),从而预防突发故障,最大限度地提高设备综合效率。
这个体系包含两个紧密相连的关键部分:
- 点检: 这是信息输入环节。如同医生的“诊断”,其唯一任务是通过人的感官和工具,按标准检查设备健康状况,回答**“设备有没有问题?严重程度如何?”**。点检的输出是数据和状态信息,是后续所有决策的基石。没有准确的点检,定修就成了无源之水。
- 定修 : 这是行动输出环节。如同医生的“治疗方案”,其核心在于“定”字,意为“预定性”或“计划性”的修复活动。它基于点检的诊断结果,来回答“我们应在何时、以何种方式修复?”。它标志着维修从被动抢修向主动规划的根本转变。因此,点检是定修的输入,定修是点检分析后的输出,两者构成了“先诊断,后治疗”的完整闭环。基于此,“定修”具体表现为两种计划性的维修形式:
- 定期维修: 基于时间的预定性维修,如“设备每运行5000小时,计划更换轴承”。
- 状态维修: 基于状态的预定性维修,如“通过点检监测到轴承振动超标,计划在下周安排更换”。
2. 追根溯源:点检定修制的起源
点检定修制的思想雏形可以追溯到上世纪50年代的日本。二战后,日本工业迫切需要快速恢复和发展,对生产效率和设备稳定性的要求极高。在这一背景下,日本企业,特别是以新日本制铁公司(简称“日钢”,Nippon Steel)为代表的钢铁企业,在引进美国预防性维修(Preventive Maintenance, PM)思想的基础上,结合本国国情,逐步发展出了一套独特的设备管理模式。
他们发现,仅仅依靠固定的时间周期进行维修,会产生“过度维修”(设备状态尚好就被拆开)或“维修不足”(隐患在周期到来前就已爆发)的问题。因此,他们强化了对设备日常状态的监控,将操作工人和专业维修人员结合起来,形成了“点检”的早期实践,并以此为依据来精确安排维修活动,最终系统化地形成了我们今天所说的“点检定修制”。
3. 宝钢的“引进来”:一场深刻的维修革命
上世纪70年代末,中国改革开放拉开序幕,决定从日本引进成套技术和设备,建设现代化的上海宝山钢铁总厂(简称“宝钢”)。宝钢不仅引进了日钢的先进设备,更重要的是,系统性地引进了其管理思想,其中就包括“点检定修制”。
在引进之初,宝钢乃至整个中国的工业企业普遍实行的是“日修制”或苏式的“计划预修制”。
- 日修制 (Day-to-day Reactive Repair): 这个名词的核心在于“日”字,意指维修工作完全由“当天(每日)”发生的突发故障所驱动。维修团队如同“救火队”,每天的工作就是处理当天出现的各种紧急故障,是一种完全被动、以事后抢修为核心的模式,严重影响生产的连续性。
- 计划预修制: 按照固定的年、月度计划对设备进行解体大修,不关心设备实际状态,导致维修成本高、周期长,且频繁的拆装本身也可能引入新的故障。
宝钢在日方专家的指导下,开启了从“日修制”向“定修制”的深刻变革。这场变革是艰难的:
- 思想观念的冲击: “设备没坏为什么要修?”“操作工只管生产,凭什么要检查设备?”这些都是当时普遍存在的疑问。宝钢通过大量的培训和实践,逐步建立了“我的设备我维护”的全员生产维护(TPM)思想。
- 组织结构的重塑: 成立了专门的点检站和专业的点检队伍,明确了操作工、点检员、维修工各自的职责,形成了“点检—分析—计划—实施—验证”的管理闭环。
- 从被动到主动的转变: 通过点检,维修工作从“救火队”变成了“保健医生”。维修人员不再是等设备坏了去抢修,而是根据点检数据,提前预判问题,制定精准的维修方案,将故障消灭在萌芽状态。
宝钢的成功实践,证明了点检定修制在提高设备OEE(综合效率)、降低维修成本、保障生产稳定方面的巨大优势,为这套体系在中国的推广树立了光辉的典范。
一个水泵的故事:两种制度,两种结局
为了更直观地理解这种转变,让我们来看一个发生在车间里的小故事:
- A车间(推行点检定修): 操作工小李在进行日常点检时,发现3号水泵的声音比平时稍微大了一点,他立刻做了点检记录并上报。专业的点检员老张接到报告后,马上用测振仪对水泵进行精密诊断,发现其轴承振动值已接近警戒线。他结合历史数据分析,判断该轴承的劣化趋势已经开始。于是,维修团队根据这个明确的诊断结果,制定了一个定修计划——在下个周末设备例行停机时,更换这台水泵的轴承。最终,维修按计划顺利完成,成本可控,生产未受任何影响。
- B车间(仍在用日修制): 他们同样型号的水泵,在上周一的生产高峰期,没有任何预兆地突然“抱死”,发出刺耳的金属摩擦声。整个车间被迫紧急停产,维修工人们像救火一样冲过去,手忙脚乱地抢修了半天,最终才恢复生产。这次事故不仅造成了巨大的生产损失,更换轴承的成本也因紧急采购而增加了不少。
这个小故事生动地展示了“保健医生”与“救火队”的天壤之别。
4. 在中国的推广:从冶金到各行各业
宝钢的成功引发了全国性的关注。原冶金工业部迅速将“宝钢经验”在全国冶金行业进行推广。各大钢铁企业如武钢、鞍钢等纷纷派人学习,结合自身情况推行点检定修制度,取得了显著成效。
随后,这股浪潮迅速扩展到其他行业:
- 石化行业: 流程长、连续性要求高的石化企业,发现点检定修制是保障装置长周期运行的法宝。
- 电力行业: 发电机组的稳定运行事关国计民生,点检定修能有效预防重大设备事故。
- 装备制造、汽车、烟草、水泥等行业也相继引入并本地化了这套体系,使其成为中国现代工业设备管理的“标准配置”。
5. 常见的误区与正确的使用方式
尽管点检定修制被广泛应用,但在实践中也存在许多误区,导致效果大打折扣:
- 误区一:定修 = 定期修。 这是最大的误解。很多企业将定修简单理解为按日历进行维修,忽视了点检的作用。结果依然是“过度维修”或“维修不足”,没有体现出状态监测的优势。
- 误区二:点检流于形式。 点检表填得满满当当,但数据无人分析,异常无人跟踪。点检变成了为了应付检查的“纸面工作”,失去了其作为决策依据的根本价值。
- 误区三:重维修,轻点检。 过于依赖维修人员的“高超技艺”,而忽视了作为第一道防线的操作工点检。实际上,80%的设备隐患都能在早期通过简单的点检被发现。
- 误区四:系统僵化,缺乏优化。 一套点检标准和定修周期“一用到底”,没有根据设备老化、工况变化进行动态调整和优化。
如何正确使用?
- 强化点检核心地位: 确保点检标准科学、执行到位、数据真实有效。建立从异常发现到闭环处理的快速响应机制。
- 推动状态修: 大力发展设备诊断技术(如振动分析、油液分析、红外热成像),将“定期修”尽可能转向基于设备实际状态的“状态修”,实现精准维护。
- 数据驱动决策: 建立设备管理数据库,对点检数据、维修历史、备件消耗进行统计分析,从中找出薄弱环节,持续优化维修策略和周期。
- 全员参与,权责清晰: 明确操作工、点检员、技术员、维修工在体系中的角色和职责,形成高效协同。
结语
从日钢的创新,到宝钢的引进,再到全国各行业的普及,点检定修制深刻地改变了中国的工业面貌。时至今日,它依然是企业设备管理不可或缺的基石。面对数字化和智能化的浪潮,它将在融合TPM、RCM等先进理念,并插上科技翅膀的背景下,继续为企业的基业长青保驾护航。