引言:为什么许多技术驱动的维护方案难以奏效
一提到智能维护,很多人首先想到的就是“预测性维护”。但这其实是一个常见的误区,甚至可能让企业在投入巨资后,发现收效甚微。为什么呢?因为在很多实际场景下,预测性维护带来的“乌龙”预警(即误报)所产生的折腾和成本,常常会吞噬掉好不容易才省下的钱。
幸运的是,智能维护的棋盘上不止有“预测”这一颗棋子。另外两种强大的策略——基于状态的维护(CBM)和高级故障排除(ATS),往往是更务实、见效更快的选择。因此,全面理解 IoT 数据与高级分析技术在维护中的所有应用,能够帮助企业明确选择最合适的技术或技术组合。
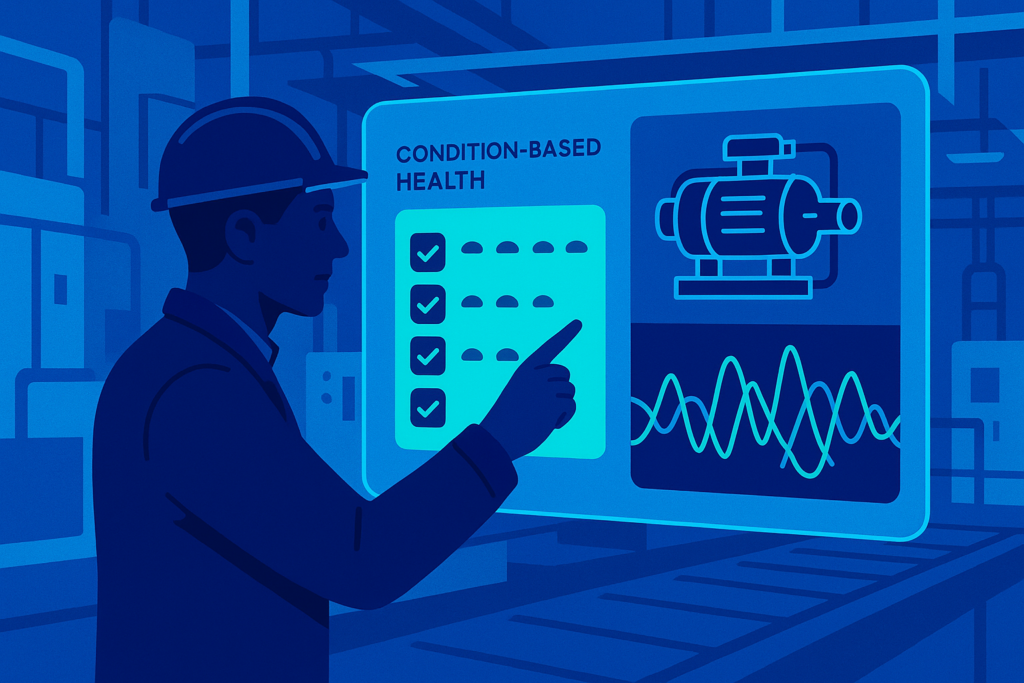
原文:Establishing the right analytics-based maintenance strategy
企业为何加大对数据的投资?
全球范围内,许多公司都在大力投资物联网(IoT)、高级分析(AA)和相关技术。根据2019年报告,超过25%的企业已开始使用物联网连接其设备,并预计在2023年,全球物联网连接设备的数量达到430亿台。物联网传感器通过收集设备的温度、振动、流量和压力等数据,配合高级分析,能够帮助判断设备的健康状况。
许多领先企业已通过这些技术,对公司的设备维护方式进行了变革。其中,最流行的方法之一便是“预测性维护”系统,它通过传感器数据加分析算法,提前预判设备潜在故障。从而可以在故障发生之前采取措施,减少停机时间。
谁不希望设备运行时间更长、故障预测性更强且服务成本更低呢?
预测性维护:看上去很美,为何常常“水土不服”?
然而,许多公司在花大钱上了预测性维护后,发现投资回报遥遥无期。
虽然提醒系统可以有效预警故障发生,但过度的预测性维护可能导致设备过早或过于频繁地停机进行维修。
尽管预测性维护通常被视为物联网和高级分析的典型应用,但事实上,所有的预测都有误差。我们的研究发现,即便一些组织拥有高水平的高级分析团队,他们的预测效果仍然难以达成预期目标。所使用的算法可能会漏掉一些故障(假阴性),或者预测一些实际上并不会发生的事件(假阳性)。尽管组织通常会花费大量精力减少假阴性,但往往假阳性是造成预测性维护失效的关键原因。
毫无疑问,预测性维护在高风险或安全性要求极高的环境中极具价值。例如,喷气发动机的故障如果发生在空中,其后果非常严重,此时预测性维护尤为重要。然而,许多商业环境并不符合这种高度可预测的条件,许多事件难以预测,而提前预测的收益往往有限。设备停机带来的麻烦无论如何都会发生,不论是设备自发故障,还是计划中的预防性停机。
【一个典型的“赔本赚吆喝”案例】 一家公司的某款设备平均每年坏4次,单次维修成本1500美元。他们费了九牛二虎之力,用预测性维护实现了对其中25%的故障进行预警,准确率高达85%,单次能节省约10%的成本。 听起来不错?管理层一算,估计每年能省下上百万美元。 但坑就坑在,这套系统有10%的误报率。 这在行业里算很优秀了,可换算下来,就是每年多出了1000次不必要的上门维修。这笔开销,正好把省下的钱全都赔了进去。更让客户头疼的是,虽然维修可以提前计划,但维修总次数反而增加了,总停机时间不降反升。
遗憾的是,这样的情况在许多企业中很普遍。
两种替代方案:更接地气,更快见效
除了预测性维护,物联网和相关技术还有两种应用可以提供更为简便且成本较低的干预方式:基于状态的维护(CBM)和高级故障排除(ATS)。虽然这两者同样依赖物联网和高级分析技术来收集和分析数据,但它们的运作方式与预测性维护有所不同。
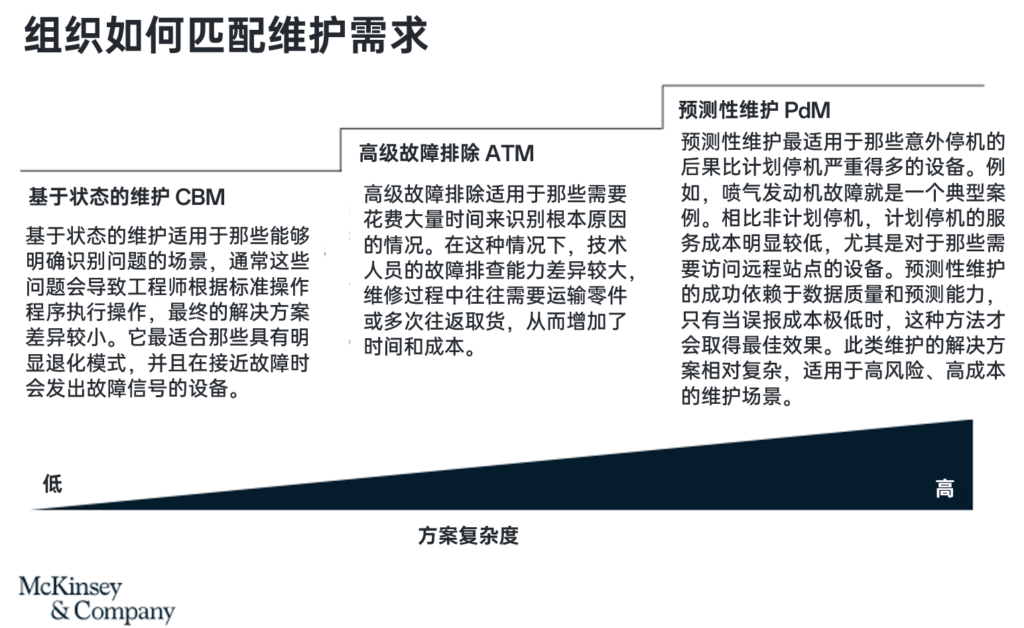
基于状态的维护(CBM):看状态,再维护
当风险较低或故障预测不够准确时,企业仍然希望密切监控设备状态,那CBM方法更简单直接。CBM通过物联网和数据分析,持续监控资产状况并确定何时进行维护。与预测性维护类似,CBM会监控关键性能参数,例如设备的温度、振动和压力等数据,帮助识别潜在问题。性能数据可以定期或是持续收集。
与传统的预防性维护相比,CBM仅在关键指标显示设备性能下降或即将发生故障时才进行维护,从而延长了设备的维护周期。
例如,一家大型科技制造商引入了CBM框架,该框架通过多个数据来源(如物联网设备、历史服务数据等)为设备提供状态监控。通过这一框架,企业能够高效响应客户服务请求,将人工成本、停机时间和零件成本减少了30%。
高级故障排除(ATS):出问题,快搞定
如果说CBM重在“防”,那么ATS则重在“治”。当设备出现故障或表现异常时,ATS技术通过分析机器数据及历史故障记录,能够帮助工程师快速确定问题根源,减少停机时间并提高设备的正常运行时间。
即使是最先进的设备,也难免会在某一时刻出现故障。传统的故障排除方式通常要求工程师上门后“蒙着采,挨个试”这不仅耗时耗力,还容易浪费不必要的零件。相较之下,ATS利用物联网和相关技术,帮助工程师远程诊断故障根本原因,减少现场修复的次数和相关成本。
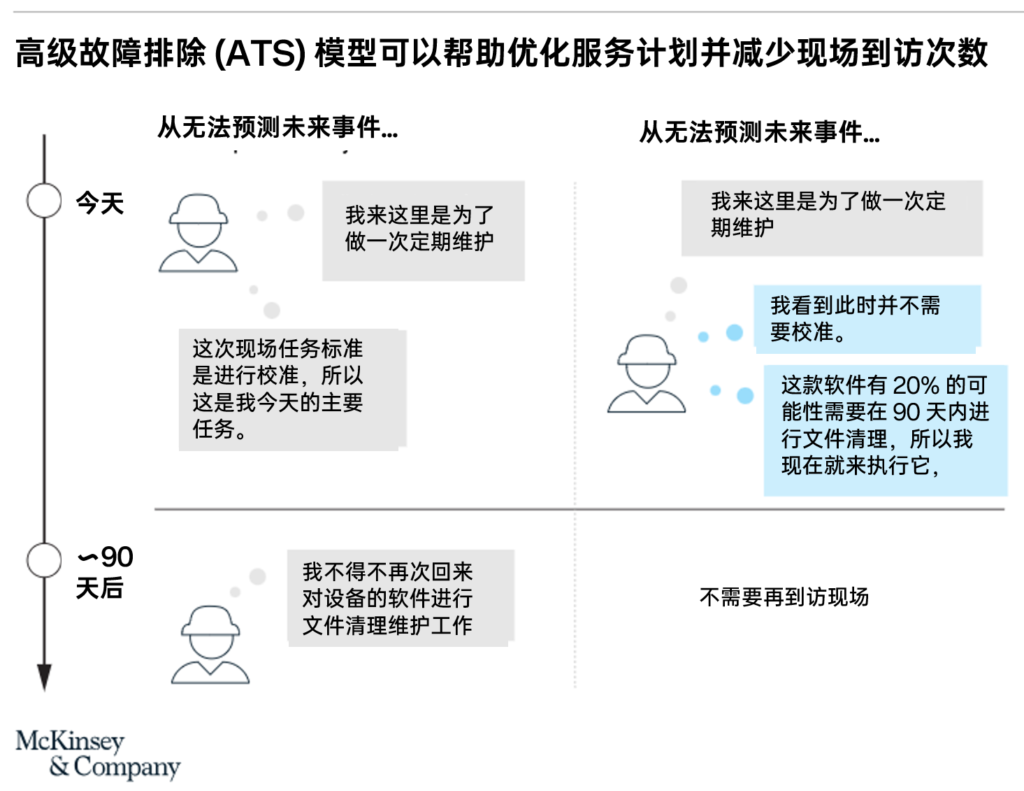
例如,一家大型医疗设备制造商开发了ATS解决方案,利用历史故障数据、传感器、日志及客户报告,快速定位设备问题。该解决方案使维护成本降低了18%到25%,并通过减少停机时间显著提高了客户体验。此外,该系统还建立了标准化的故障排除流程,从远程故障排除开始,只有在无法解决的问题才会安排现场维修。
ATS的改进同样提高了远程问题解决率,类似于IT服务商通过电话为客户提供技术支持。引入ATS后,解决问题的平均时间(AHT)减少了40%。
总结:用好数据,只需“化繁为简”四步走
要真正发挥数据在维护领域的价值,不一定非要从最复杂的预测性维护开始。以下四个更简单的步骤,能帮助任何企业走上正轨:
- 先从CBM和ATS入手,小步快跑。 这两种方法见效更快,能帮你迅速看到成果,建立信心,并用省下来的钱为未来更复杂的分析模型“储备弹药”。
- 让业务专家和数据专家“肩并肩”工作。 算法不能闭门造车。数据科学家负责建模,但模型是否靠谱、方案是否可行,必须由懂行的业务专家来验证和把关。
- 打造“信数据、用数据”的文化氛围。 技术转型的最大阻力往往来自人。关键是要让从领导到一线的每一位员工都理解并相信数据能让他们的工作更轻松、更有价值,而不是把它看作是麻烦。
- 建立有效的数据采集机制。 巧妇难为无米之炊。没有持续、可靠的数据(无论是来自传感器还是手工记录),再好的算法都是纸上谈兵。
归根结底,智能维护是一场持久的转型。最好的路径不是一步到位,而是由简入繁,从小处着手,稳步推进。